Our ISO/IEC 17025 accreditation has been extended!
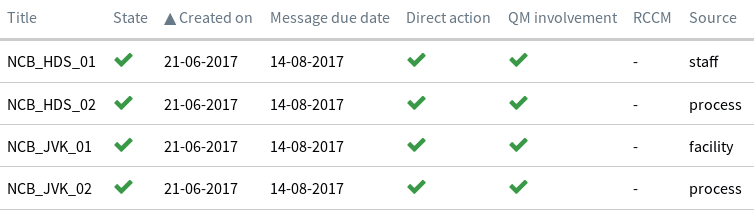
We are very pleased to have received the ISO/IEC 17025 accreditation once again. The Raad van Accreditation (RvA), the Dutch institute for accreditation, visited our lab in Amersfoort and audited plus accredited our calibration services.
We have been audited and accredited already for the last 29 years. Still, every year the accreditation process requires our focus and time as ISO/IEC 17025 requirements keep changing and improving. In comparison to last year, we improved a number of our processes as required.
General accreditation process
An ISO/IEC 17025 accredited laboratory in the Netherlands is subject to the below auditing cadence by our accrediting body, the RvA:
- Yearly global audit with one team leader and one technical expert per quantity. The yearly audit focusses in depth on specific topics of ISO/IEC 17025.
- 4 yearly full re-evaluation again with one team leader and technical expert per quantity. The re-evaluation reviews the full (for now still section 4 and 5) ISO/IEC 17025 standard.
'Non Conformities' result in improved procedures
The RvA aims to be a partner who helps you to improve your management system. It is my personal experience this really is the case. This year, we’ve had the RvA audit C07.1. This means it is the first yearly audit of our seventh 4-yearly cycle, so you can say we do have a lot of experience!
Audits so far have always been positive and accredited. Still, we do receive Non Conformities (NCF’s). These help us to improve our calibration process, to become even more traceable and improve our carefree service to our customers. Our whole calibration process was audited, from communication to traceability, which resulted in a few NCF’s.
This year’s NCF’s
We register and monitor our NCF’s in our enterprise resource planning system under section K048-C07. When entered, we mark them and after solving it, we mark it with a
.
This year, we had a total of 4 NCF’s. They all are weighed to have a Quality Manager involvement, but are not as severe to have a Root Cause Counter Measurement (RCCM) action. A RCCM would have meant a fierce reorganization of our processes.
Example NCF: external calibrations
One of the NCF's we received concerned our external calibrations: instruments we receive that again are sent to an external lab with a complementary scope. The NCF mentioned the communication to our customers about this process. The recommendation was to make it absolutely clear to our customers which path their instrument had taken.
We register this NCF and the follow up can be traced and reported in detail through our NCF module as seen in this example:
Recording and monitoring the NCF’s in this way, makes the processing very effective and manageable ergo reduces the maintenance costs of our accreditation. The result also proofs that our approach is right: the RvA has accepted our changes and accredited us once again!
About the Raad van Accreditatie, the accrediting body
As seen in many European countries, the Dutch Council for Accreditation (RvA) started as part of our National Metrological Institute (NMI) which by definition is technically oriented. Nowadays the RvA is mainly focused on quality and technical competence, it is sourced from third parties like experts from our NMI, university or commercial companies. View our scope here on the website of RvA or read more about our worldwide accreditation
Questions?
Please contact me.
Carel Adolfse
Technical Director
oktober 26, 2017