Customer case Blanken Controls
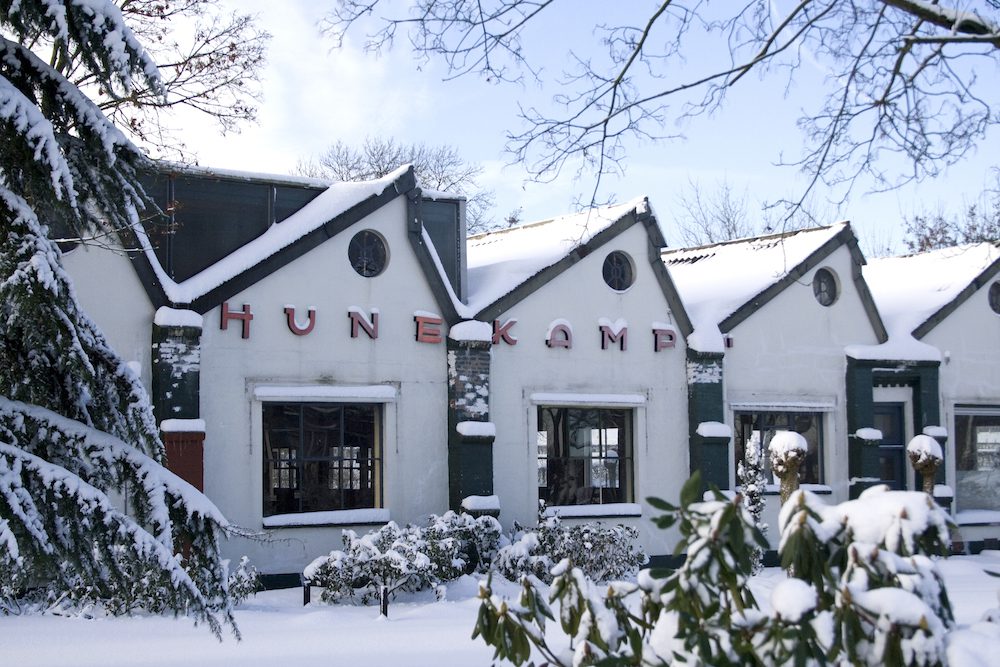
For many years Blanken Controls in the Netherlands has been one of Minerva’s valued customers. Blanken Controls recently chose to implement a new calibration management system, MET/TEAM. Erik van Asselt, Managing Director of Blanken Controls elaborates why he appreciates the cooperation, and the way Minerva has helped to implement MET/TEAM.
We help our customers with compliance
What does Blanken Controls do?
“Blanken Controls has been around for 43 years and is a wholesaler of measurement and control technology, expanded with a service and calibration facility. The common thread in our business is that we help our customers with compliance; so that they comply with laws and regulations. We provide calibration, asset management and repair services.
We work for installation companies who increasingly must deal with laws and regulations. We help our customers to comply with laws and regulations throughout the chain. For example, an air conditioning installation company needs a personnel certificate and a company certificate. We advise in the certification process and supply the right tools in accordance with the previously mentioned laws and regulations. Complete with the correct certificates, associated maintenance schedules and recalibrations. In the installation contracting market, we like to answer our customers' questions before they feel the need to ask questions. We recently became a partner of branch organization Techniek Nederland to help installation companies meet the requirements when transitioning to heat pumps.
Blanken Controls is also active in the food industry as we work for large supermarkets and fast food chains that must comply with HACCP legislation. We supply them with thermometers with the right certificates”.
High-end market and short communication-lines
What can you tell us about the collaboration with Minerva?
“Blanken Controls and Minerva have been working together for quite some time now. We hire Minerva for the recalibration of our own calibration standards. Minerva is a great company that operates in the high-end market and has short communication-lines.
In 2021 and 2022, we went through a change process with Minerva. In concrete terms, this concerns the migration from MET/TRACK to MET/TEAM; both calibration software from Fluke. It was a major investment, and such a software upgrade changes a lot in the organization. You want to be well prepared for that”.
Switch to a more modern system
What prompted you to look for new calibration software?
“Our calibration and registration software are our process and form the heart of our service department. The software we used, MET/TRACK, was outdated. We could not connect with other systems, and we could no longer update thus the security was not optimal. We just felt that we had to switch to a more modern system.”
Why did you choose Minerva when choosing calibration software?
“We considered several options. Choosing Minerva was strongly connected to our choice to opt for Fluke’s MET/TEAM software and its features. That choice allowed us to stay with Fluke and keep using the same database. As we had already contacted Minerva as Fluke’s distributor, working with Minerva was the logical choice. We also had regular and good contact with Siebe Borger from Minerva; the conversations were nice and there was trust. The feeling was good.”
Constructive, cooperative and helpful attitude
How did the implementation go after choosing Minerva?
“All in all, we have been working on the entire process for about a year, we started in September 2021 and went live in the summer of 2022.
We spent a lot of time preparing for the migration. We've had quite a few sessions with Minerva. The idea from the start was to first get the basics right and only use the current functionalities, so not all of them. The most important thing was that our calibration technicians could work well with the software. We have quarantined MET/TRACK, the old system for the migration. The entire process with Minerva went smoothly.
Nevertheless, there are always points that emerge in such an implementation. It is a big change anyway and new software always takes some getting used to. And where work is done, mistakes are made. That's no more than normal. We were satisfied with the training and they did everything they could to get our people to work with the new system”.
Personal attention made a difference
Which moments have stayed with you most in the collaboration with Minerva in this process?
“I really liked the constructive, cooperative and helpful attitude. Sometimes we had other ideas ourselves, but Minerva was certainly open to that. What I also really liked is the transparency and approachability of Minerva. For example, the employees of Blanken Controls simply e-mailed directly with the employees of Minerva. This is also good for mutual commitment and accountability. The personal attention that Minerva gave made a difference. But the most important thing is that our primary process is guaranteed after going live. Minerva helped us very well with that”.
December 1, 2022